
رنگ های بر پایه اپوکسی
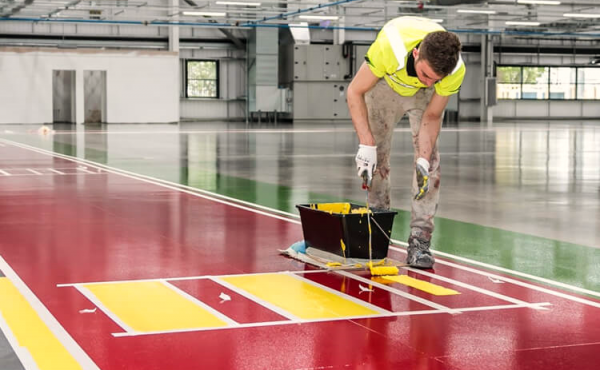
رنگ اپوکسی یکی از بهترین، سخت ترین و بادوام ترین مواد رنگی است که در بازار موجود می باشد. بیشتر آن ها به صورت یک سیستم دو جزئی (۲K ) عمل می کنند و کابردهای متعددی دارند. رایج ترین کاربرد آن ها پوشش سطوح سیمانی، بتنی، سازه های فلزی و کف پوش های چوبی است. رنگ اپوکسی می تواند به عنوان یک آب بند بر روی کفپوش های سیمانی عمل کند و هم چنین بر براقیت و درخشش کفپوش ها بیفزاید. عمدتا از آن برای رنگ آمیزی کف گاراژها و زیر زمین ها استفاده می شود. یکی از مهم ترین کاربردهای این رنگ، پوشش لوله ها و مخازن آب و روغن است.
رزین ها:
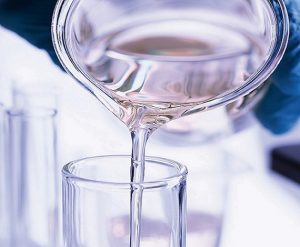
یکی از مشخصه های اصلی رنگ ها، رزین های مورد استفاده در فرمولاسیون تولید هستند که در گروه بندی و نام گذاری رنگ ها نیز از نام آن ها استفاده می شود. رزین ها مانند یک چسب عمل کرده و دیگر اجزای رنگ را به یکدیگر پیوند می دهند. گاها از رزین ها با نام حامل نیز یاد می شود. پیوند دهنده ها یا رزین ها به دو گروه تقسیم می شوند. گروه اول پیوند دهنده های تغییر پذیر هستند که به طور کامل پلیمریزه نمی شوند. در این گروه از رنگ ها فرآیند پلیمریزاسیون به صورت جزئی انجام شده و ادامه ی فرآیند در حین انجام کار و تشکیل فیلم رنگ کامل می شود. رنگ های اپوکسی، پلی اورتان و آکریلیک های ترموست از جمله رنگ های تغییر پذیر هستند. گروه دوم رزین های غیر قابل تغییر هستند که پیش از استفاده فرآیند پلیمریزاسیون به طور کامل انجام می شود. استفاده از این نوع رزین در مقایسه با گروه اول متداول نبوده و به عنوان مثال می توان از رزین های سلولزی و نیتروسلولزی نام برد.
اجزای تشکیل دهنده رنگ :
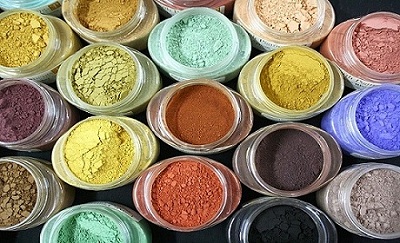
۱- رنگدانه :
رنگدانه ها یا پیگمنت ها ذرات معلق کوچکی هستند که در رنگ توزیع شده اند و ویژگی های خاصی از جمله رنگ، کدورت، دوام، استحکام مکانیکی به رنگ می بخشند. برخی از رنگدانه ها مانع از خوردگی و زنگ زدن بسترهای فلزی می شوند. می توان آن ها را به دو گروه رنگ های آلی و غیر آلی تقسیم کرد. دسته ی اول ریشه در طبیعت داشته و برگرفته از خاک، سنگ، گیاهان و یا حیوانات هستند و تنها جنبه ی دکوراتیو داشته و موجب دست یابی به توناژ مورد نظر و رنگ دهی به محصول می شوند. گروه دوم رنگدانه هایی هستند که ساخته ی دست بشر بوده و در آزمایشگاه تولید می شوند. این رنگ ها که با نام رنگ های متالیک نیز شناخته می شوند علاوه بر زیبایی، حفاظت از بستر را به همراه دارند.
حلال هیدروکربنی رزین اپوکسی را در خود حل می کند، به نفوذ رنگ درون بستر بتونی کمک میکند، جریان پذیری آن را بهبود می بخشد و موجب تشکیل یک فیلم یک نواخت از رنگ با پوشش دهی مناسب می شود. رنگ های اپوکسی بر پایه حلال کف زمین، سرعت خشک شدن و سخت شدن بالایی دارند و در برابر سایش و مواد شیمیایی مقاوم هستند.
رنگ های اپوکسی برپایه حلال عموما به صورت تک جزئی و رنگ های اپوکسی فاقد حلال غالبا به صورت دو جزئی در بازار عرضه می شوند. ساختار رنگ های اپوکسی بر پایه حلال با رنگ های فاقد حلال خیلی متفاوت نیست. در رنگ های فاقد حلال ویسکوزیته اندکی بیشتر است و اختلاط و استفاده از رنگ به ویژه در فصول سرد سال اندکی دشوار است. یکی از راه های غلبه بر این مشکل استفاده از رقیق کننده های فعال است که تنظیم شدن ویسکوزیته و پخت پوشش دهنده کمک می کند. به طور کلی اپوکسی های فاقد حلال نسبت به پوشش دهنده های اپوکسی بر پایه حلال غلیظ تر هستند و استفاده از سخت کننده های پلی آمید به آن ها ترجیح داده می شود.
۲- حلال :
حلال ها دومین جز مهم در تولید رنگ ها هستند و هدف از استفاده از آن ها جریان پذیری رنگ و حل کردن رزین و سایر اجزای رنگ است. انتخاب نوع حلال وابسته به عوامل مختلفی از جمله دیگر اجزای به کار رفته در فرمولاسیون رنگ، هزینه ی تمام شده و ایمنی در حین کار است. دومین عامل مهم در انتخاب نوع حلال، نرخ تبخیر آن است. برخی از آن ها نرخ تبخیر پایینی دارند و یک مدت زمان باز بودن در اختیار فیلم رنگ قرار می دهند در حالی که برخی دیگر به سرعت تبخیر می شوند. معمولا حلال هایی که نرخ تبخیر بالایی دارند برای رنگ ها گزینه ی مناسب تری هستند. حلال ها انواع مختلفی دارند و می توان آن ها را بر اساس کارکرد و یا ساختار شیمیایی شان دسته بندی کرد. در میان این حلال ها، حلال های هیدروکربنی آروماتیک مانند زایلن و تولوئن و از جمله حلال های قوی که نرخ تبخیر بالایی دارند مانند استون، متیل اتیل کتون (MEK) و متیل ایزوبوتیل کتون از حلال های متداول در صنعت رنگ های اپوکسی هستند. برای پاک کردن رنگ های اپوکسی از روی سطوح شیشه ای و پلاستیکی از حلال ایزوپروپیل الکل استفاده می شود. در رنگ های اپوکسی بر پایه حلال که برای رنگ آمیزی کف زمین استفاده می شوند از حلال های هیدروکربنی مانند زایلن استفاده می شود.
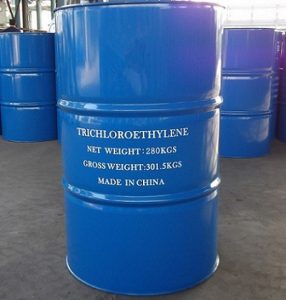
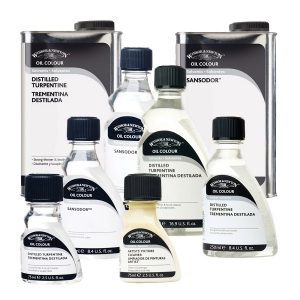
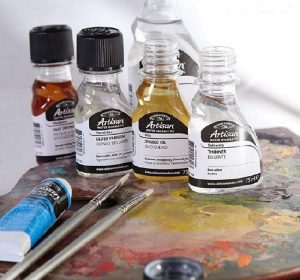
۳- پرکننده :
پرکننده ها در واقع نوعی افزودنی هستند که به دلیل استفاده از مقادیر زیادی از آن ها، می توان به عنوان یک جز اصلی و مستقل آن ها را در نظر گرفت. پرکننده ها انوع مختلفی دارند و علاوه بر نقش اصلی خود می توانند چند کار دیگر را به صورت مشترک انجام دهند. به عنوان مثال آلومینا سه آبه (AI2O3•۳H2O ) یک پرکننده است که از اشتعال پذیری نیز جلوگیری کرده و آن را به تعویق می اندازد. رایج ترین پرکننده ها کلسیم کربنات، طلق یا تالک، سیلیکا، والاستونیت، خاک رس، کلسیم سولفات، میکا، افزودنی های با ساختار شیشه ای و آلومینا تری هیدرات (ATH) هستند. پرکننده ها اهداف مختلفی از جمله کاهش هزینه ی تمام شده را دنبال می کنند. برخی از پرکننده های اپوکسی عبارتند از :
میکروبالون ها:
این پرکننده ی سبک اپوکسی شامل میکروسفرهای پلاستیکی (فنولیک) و شیشه ای است که با اپوکسی مخلوط شده و یک ترکیب سبک را ایجاد می کند که به راحتی شکل پذیر است. برای جلوگیری از سرخوردن محصول از روی سطوح عمودی می توان آن را با سیلیکا کلوئیدی مخلوط کرد.
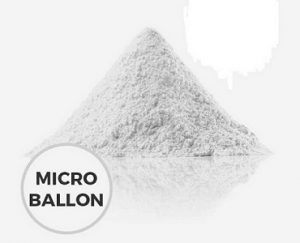
پودر چوب :
این پرکننده ی رزینی یک پودر ریز ساخته شده از چوب های پودر شده است که افزودن آن به اپوکسی باعث تشکیل یک مخلوط چسبنده ی قوی می شود. برای سهولت در سنباده کشی آن را با میکروبالون ها ترکیب می کنند و برای جلوگیری از سرخوردن از بسترهای عمودی از سیلیکای کلوئیدی کمک می گیرند. اپوکسی های ترکیب شده با پودر چوب برای پوشش بسترهای چوبی گزینه ی مناسبی هستند زیرا این پودر اپوکسی را به رنگ چوب در می آورد. برای تطبیق رنگ مخلوط با بسترهای چوبی مختلف از رنگ دانه ها استفاده می شود.
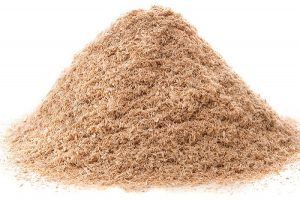
سیلیکا کلوئیدی :
سیلیکا کلوئیدی که با نام های سیلیکای تغلیظ کننده و اکسید سیلیکون نیز شناخته می شود یک پودر سفید رنگ با دانه های کوچک است. مخلوط کردن مقادیر بسیار کمی از آن با اپوکسی موجب دستیابی به نتیجه مطلوب می شود و با دیگر پرکننده ها نیز قابل اختلاط است.
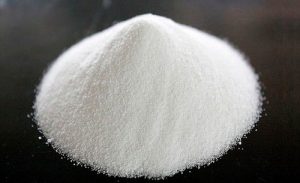
الیاف شیشه خرد شده :
آن ها رشته های فایبر گلاس ریز آسیاب شده هستند که جهت تغلیظ اپوکسی و پر کردن شکاف ها افزوده می شوند. این الیاف پرکننده ی اپوکسی موجب افزایش استحکام و حداکثر مقاومت در برابر ترک خوردگی می شوند. این پرکننده پس از پخت سطحی ناصاف و ناهموار ایجاد می کند و در مواردی که صیقلی بودن سطح برای ما اهمیت دارد گزینه ی مناسبی نیست. در صورت لزوم می توان از سیلیکا کلوئیدی برای جلوگیری از ریزش ترکیب از روی بسترهای عمودی استفاده کرد. با افزودن میکروبالون ها به مخلوط، سنباده زدن آن نیز بهتر می شود.
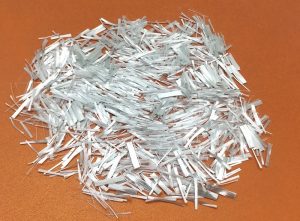
۴- افزودنی :
اگرچه درصد آن ها در رنگ بسیار اندک است اما در بهبود خواص آن تاثیر بسزایی دارند. از جمله افزودنی ها می توان به ترکیبات جلوگیری کننده از ایجاد فوم، و جلوگیری کننده از ترک خوردن و پوسته شدن رنگ، تغلیظ کننده ها، خشک کن ها و … اشاره کرد.
۵- رزین :
رزین ها مانند یک چسب و یا پیوند دهنده تمام اجزای رنگ را در کنار یکدیگر نگاه می دارند و موجب اتصال آن ها به یکدیگر می شوند. عموما ترکیب مخلوط رزین و حلال، حامل نامیده می شود. رزین ها از مشخصه های اصلی رنگ ها هستند و رنگ ها بر اساس نوع رزین به کار رفته به گروه های مختلفی تقسیم می شوند. از جمله رزین های مورد استفاده در صنعت رنگ می توان به رزین های اپوکسی، پلی اورتان و نیتروسلولزی اشاره کرد.
رزین اپوکسی:
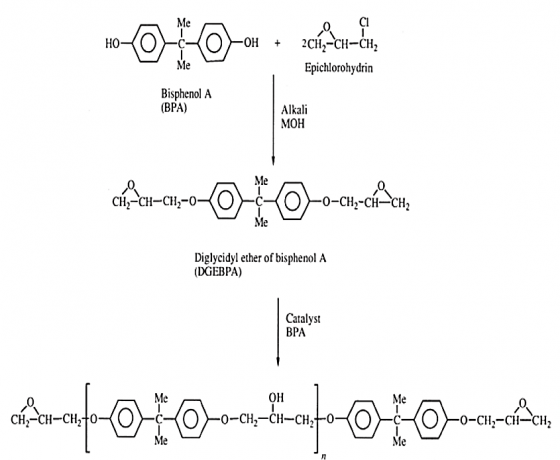
رزین های اپوکسی با نام هایی مانند araldite و epon به وسیله ی تامین کنندگانی مانند Dow plastics، Epic resins، Resyn corp. ، Shell chemicals و united resin corp. در بازار مبادله می شوند.
انواع رزین های اپوکسی :
- رزین های بیسفنول آ :
اکثر رزین های اپوکسی حاصل تراکم بیس فنول آ و اپی کلروهیدرین هستند. بسته به نسبت بیس فنول آ به اپی کلروهیدرین رزین هایی با طول زنجیره ی متفاوت به دست می آیند که از نظر جرم مولکولی، ویسکوزیه، انحلال پذیری و اجزای پوکسی و گروه های هیدروکسیل متفاوت هستند. آن هایی که جرم مولکولی کم دارند مایع هستند و گروهی که دارای جرم مولکولی متوسط تا زیاد هستند در دمای اتاق به شکل جامد هستند. رزین های با جرم مولکولی کم و متوسط برای پوشش دهی خوب به یک جفت و پارتنر برای واکنش نیاز دارند. رزین های با جرم مولکولی زیاد قدرت اتصال فیزیکی خوبی دارند، سریع خشک می شوند و عموما به عنوان آستر استفاده می شوند. این رزین ها گروه های اپوکسی کم و گروه های هیدروکسیل زیادی دارند. گروه های هیدروکسیل می توانند در دمای اتاق با پلی ایزوسیانات ها و در دمای ۱۸۰ تا ۳۰۰ درجه سانتی گراد با رزین های آمینه و رزین های فنولی واکنش دهند.
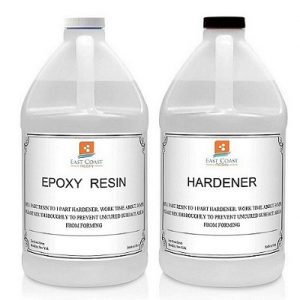
خواص رزین های اپوکسی :
رزین های اپوکسی چندین ویژگی خوب از جمله کشش بالا، مقاومت عالی در برابر مواد شیمیایی، خوردگی، چروک پذیری اندک، عایق بودن در برابر الکتریسیته، قابلیت پخت در گستره ی دمایی وسیع، نیروی چسبندگی عالی به بسترهای مختلف از جمله فلزات ( در صنایع تولید کننده ی پوشش دهنده ها این ویژگی اهمیت به سزایی دارد) و … دارد.
پخت رزین های اپوکسی:
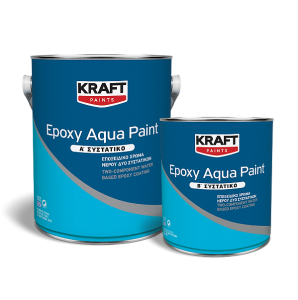
همان طور که گفته شد رزین های اپوکسی وابسته به نوع عامل پخت استفاده شده می توانند در گستره ی دمایی مختلفی پخته شوند. برخی از عوامل پخت رزین اپوکسی عبارتند از آمین های آلیفاتیک، آمین های آروماتیک، انیدرید اسید و عوامل پخت کاتالیستی. هنگام استفاده از رزین های اپوکسی در صنعت تولید رنگ و پوشش دهنده از عوامل پخت آمین های آلیفاتیک و عوامل پخت کاتالیزوری استفاده می شود. پخت رزین های اپوکسی با استفاده از آمین های آلیفاتیک مانند دی اتیلن تری آمین (DETA) در دمای اتاق اتفاق می افتد اما پخت در چنین دماهای پایینی معایب خود را دارد. از جمله این معایب کوتاه شدن طول عمر مفید و محدود بودن جرم در فرآیند پخت برای جلوگیری از پوسیدگی، ترک خوردگی و یا نیمه سوز شدن رزین در سیستم است. هم چنین رزین های پخته شده با این روش در دماهای بالا تمایل به تخریب و تجزیه شدن دارند. برای پیشرفت و بهبود محصول نهایی از یک عامل پخت دیگر، یک عامل پخت کاتالیستی مانند بنزیل دی متیل آمین (BDMA) استفاده می شود که رزین اپوکسی را در دمای ۱۰۰ درجه ی سانتی گراد میپزد و دیگر معایب استفاده از آمین های آلیفاتیک مانند جرم محدود در پخت رزین، از بین می روند.
نمونه ای از اجزای تشکیل دهنده ی یک رنگ اپوکسی دو جزئی و سخت کننه ی مورد استفاده در جدول زیر آورده شده است :
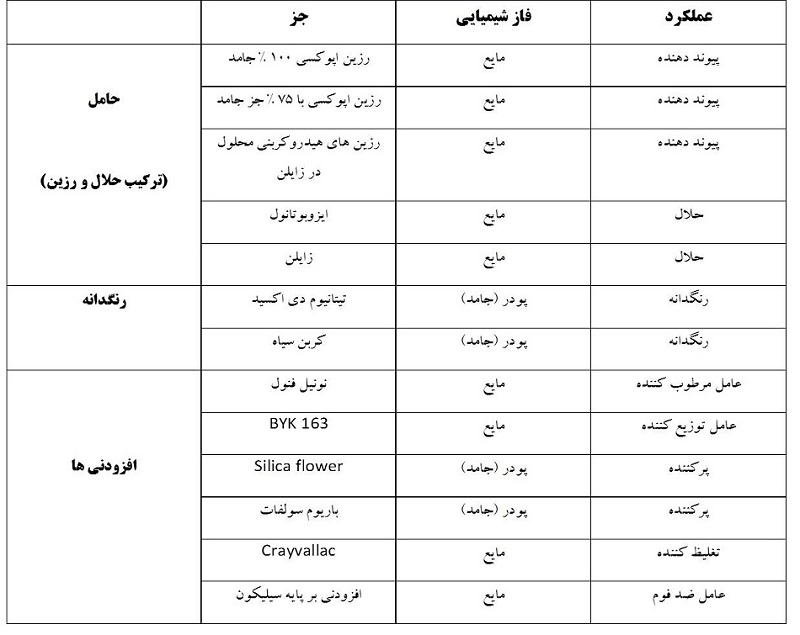
ترکیبات سخت کننده ی اپوکسی :
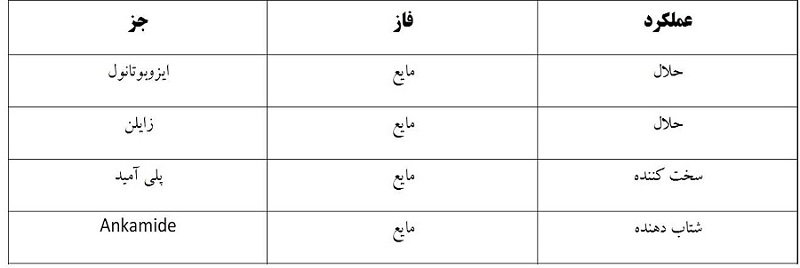
کاربرد رنگ های اپوکسی:
- رنگ آمیزی دیوار ها و کف اتاق های عمل بیمارستان ها، آزمایشگاه ها، حمام و سونا، و مکان های نگه داری، آماده سازی و جابجایی مواد غذایی به دلیل مقاومت در برابر رطوبت و باکتری
- پوشش سطوح فلزی مانند سطوح لوله ها، تانک ها و مخازن مشتقات نفتی
- پوشش کف گاراژ، زیر زمین و پاسیو به دلیل درخشش
- پوشش و محافظت از سازه های بتنی
- پوشش سطوح فلزی
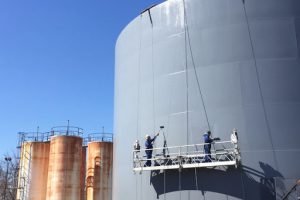
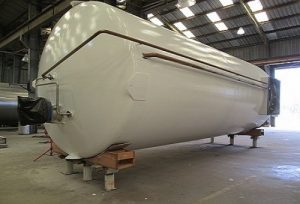
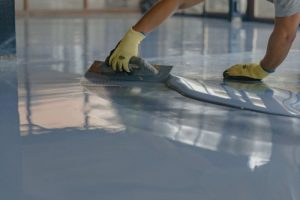
تفاوت میان رنگ ها و پوشش دهنده های بر پایه اپوکسی:
برخی به اشتباه پوشش دهنده های بر پایه اپوکسی را با رنگ های اپوکسی مشابه یکدیگر می دانند و آن ها را جایگزین یکدیگر می کنند در حالی که تفاوت هایی میان آن ها وجود دارند. به عنوان مثال پوشش دهنده های بر پایه اپوکسی از دو ماده ی سخت کننده ی پلی آمین و رزین اپوکسی تشکیل می شوند در حالی که عموما رنگ های اپوکسی از آکریلیک لاتکس ساخته می شوند و بسته به نوع محصول مقدار های متفاوتی از اپوکسی به محصول افزوده می شود. پیش از استفاده از پوشش دهنده ها لازم است تا نیروی کار دو ماده ی سخت کننده و رزین را که در دو ظرف جداگانه هستند، با یکدیگر ترکیب کند ولی رنگ های اپوکسی به صورت تک جزئی و در یک ظرف در بازار عرضه می شوند. یک تفاوت دیگر بین آن ها این است که پوشش دهنده ی بر پایه اپوکسی پخته می شود اما رنگ های اپوکسی خشک می شوند.
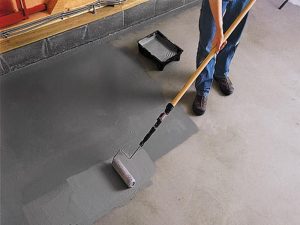
افزودن اپوکسی موجب می شود تا رنگ به بسترهایی مانند بتن بهتر بچسبد و دوام سطح افزایش یابد. چنانچه اپوکسی در فرمولاسیون افزوده نشود، رنگ به ویژه در مکان های پر تردد پوسته شده و ترک می خورد. اگر از پوشش دهنده های اپوکسی ۱۰۰ درصد جامد بر روی بستر استفاده شود، سطح سخت و بادوام شده و در برابر ترکیبات شیمیایی، سایش، ضربه، روغن، چربی و لکه ها مقاوم می شود. رنگ های اپوکسی با گذشت زمان کثیف شده و ترک می خورند در حای که پوشش دهنده ها اینگونه نیستند.
پوشش دهنده های اپوکسی بهترین گزینه برای کف پوش های با کارایی بالا هستند. این پوشش دهئده ها برای کف گاراژها گزینه ی مناسبی هستند زیرا باید گرمای تایر ماشین ها، نشتی روغن و … را تحمل کنند. آن ها هم چنین برای کفپوش های صنعتی، کف انبارها، رختکن ها و سایر مکان های پر رفت و آمد گزینه ی مناسبی هستند.
فرآیند تولید رنگ :
پیش از هرکاری لازم است تا محفظه ی اختلاط به وسیله ی حلال تولوئن یا حلال های دیگر شسته شده و به خوبی تمیز شود تا مواد باقی مانده از فرآیند قبلی از بین بروند. پس از آن از یک واحد اختلاط کوچک برای مخلوط کردن مقداری از رزین هیدروکربنی و مقداری برابر با حلال تولوئن یا حلال های مناسب دیگر، استفاده می کنیم. این فرآیند تقریبا ۳۰ دقیقه زمان می برد. سپس رزین های اپوکسی به واحد اصلی اختلاط وارد می شوند. علاوه بر رزین ها حلال زایلن، نونیل فنول و ایزوبوتانول نیز وارد شده و فرآیند اختلاط آغاز می شود. اجزای واکنش به مدت ۳۰ تا ۴۵ دقیقه با یکدیگر مخلوط می شوند تا دمای مخلوط به ۶۰-۵۰ درجه ی سانتی گراد برسد که برای افزودن ماده ی تغلیظ کننده و ضد رسوب دمای مناسبی است. بعد از دستیابی به دمای اختلاط مطلوب، سایر اجزای رنگ های بر پایه اپوکسی مانند رنگ دانه، پرکننده، عامل توزیع کننده و افزودنی ها اضافه می شوند. در این مرحله مدت زمان اختلاط ۳۰ دقیقه است. در این مرحله نمونه ای برای بررسی کیفیت به آزمایشگاه ارسال شده و سپس ماده ی ضد فوم افزوده می شود.
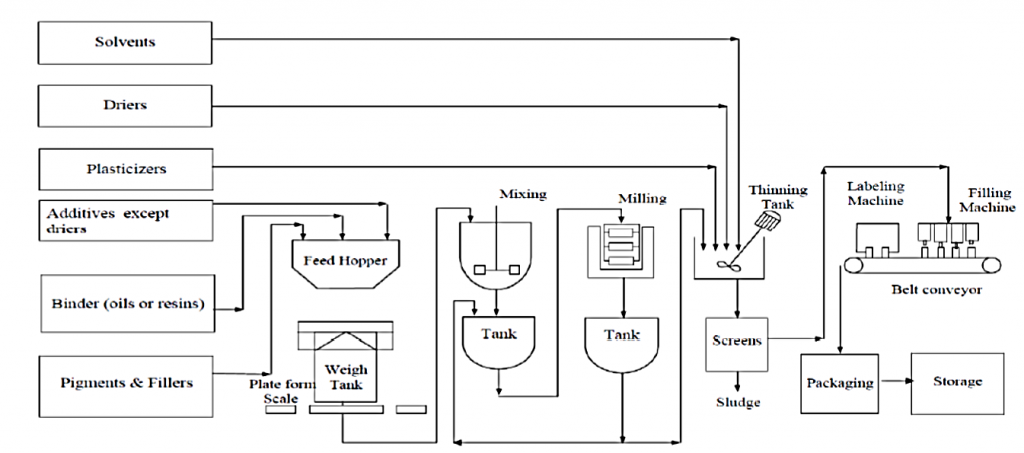