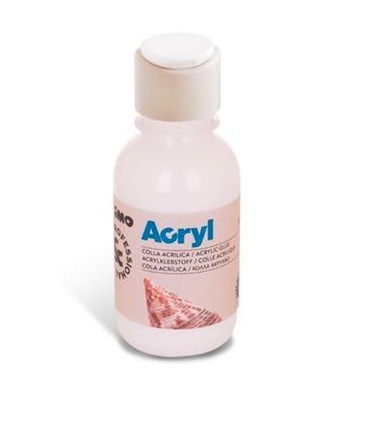
چسب های آکریلیک
چسب های آکریلیک از جمله چسب های ساختاری ترموست بوده که با چسب های اپوکسی و پلی اورتان رقابت می کنند و ویژگی های منحصر به فرد خود را دارند. آکریلیک های ترموست، چسب های فعال متاکریلیک هستند که، نسبت به دیگر رزین های آکریلیک مورد استفاده در چسب های حساس به فشار، متفاوت هستند. متداول ترین نوع آن، چسب آکریلیک سیانوآکریلات است که عموما با نام چسب قطره ای شناخته می شوند. پلیمرهای چسب های آکریلیک در هر دو حالت امولسیون آبی و محلول در حلال، به طور گسترده به عنوان پلیمر پایه در چسب های نواری حساس به فشار، برچسب ها و سایر محصولات دکوراتیو حساس به فشار مورد استفاده قرار می گیرند.
ترکیبات آکریلیک به طور گسترده به عنوان یک جز الاستومر و افزایش دهنده چسبندگی در تولید چسب های ساختمانی، چسب های لمینت و بسته بندی استفاده می شوند. در برخی موارد بخش پلی آکریلات این چسب ها کوچک بوده و به الاستومرهای دیگری مانند استایرن- بوتادین لاتکس (styrene-butadiene latex) و ترکیبات پلی وینیل استات (polyvinyl acetate) به عنوان تغلیظ کننده نیاز است. طیف گسترده ای از چسب های لمینت خاص، در هر دو حالت پر و نیمه پر از الاستومرهای آکریلیک برای اتصال سطوح غیر مشابه طی فرآیند لمینت مرطوب (wet laminating)، لمینت حساس به فشار(pressure sensitive laminating)، اتصال تماسی(contact bonding) و عملیات آب بندی حرارتی استفاده می کنند.
از ویژگی های بارز این چسب ها استحکام پیوندی قوی است؛ تا جایی که در رابطه با بسترهای پلاستیکی، شکست بستر پیش از شکست پیوندها در چسب رخ می دهد. پخت چسب های آکریلیکی در دمای اتاق و با سرعت مطلوب انجام می شود و برای اتصال فلزات، کامپوزیت ها، پلاستیک ها و … مناسب هستند. منحصر به فرد بودن آن ها برگرفته از پخت سریع آن ها در دمای اتاق است. مقاومت خوب کششی، برشی، مقاومت در برابر ضربه و مقاومت شیمیایی مطلوب از دیگر ویژگی این چسب های ترموست است. در چسب های آکریلیک فرآیند پخت به روش پلیمریزاسیون رادیکال های آزاد (Free radical polymerization) انجام می شود. در حالی که مکانیسم پخت در چسب های پلی اورتان و اپوکسی، پلیمریزاسیون تراکمی (Condensation Polymerization) است.
چسب های آکریلیک از جمله چسب های ساختاری ترموست بوده که با چسب های اپوکسی و پلی اورتان رقابت می کنند و ویژگی های منحصر به فرد خود را دارند. آکریلیک های ترموست، چسب های فعال متاکریلیک هستند که، نسبت به دیگر رزین های آکریلیک مورد استفاده در چسب های حساس به فشار، متفاوت هستند. متداول ترین نوع آن، چسب آکریلیک سیانوآکریلات است که عموما با نام چسب قطره ای شناخته می شوند. پلیمرهای چسب های آکریلیک در هر دو حالت امولسیون آبی و محلول در حلال، به طور گسترده به عنوان پلیمر پایه در چسب های نواری حساس به فشار، برچسب ها و سایر محصولات دکوراتیو حساس به فشار مورد استفاده قرار می گیرند.
ترکیبات آکریلیک به طور گسترده به عنوان یک جز الاستومر و افزایش دهنده چسبندگی در تولید چسب های ساختمانی، چسب های لمینت و بسته بندی استفاده می شوند. در برخی موارد بخش پلی آکریلات این چسب ها کوچک بوده و به الاستومرهای دیگری مانند استایرن- بوتادین لاتکس (styrene-butadiene latex) و ترکیبات پلی وینیل استات (polyvinyl acetate) به عنوان تغلیظ کننده نیاز است. طیف گسترده ای از چسب های لمینت خاص، در هر دو حالت پر و نیمه پر از الاستومرهای آکریلیک برای اتصال سطوح غیر مشابه طی فرآیند لمینت مرطوب (wet laminating)، لمینت حساس به فشار(pressure sensitive laminating)، اتصال تماسی(contact bonding) و عملیات آب بندی حرارتی استفاده می کنند.
از ویژگی های بارز این چسب ها استحکام پیوندی قوی است؛ تا جایی که در رابطه با بسترهای پلاستیکی، شکست بستر پیش از شکست پیوندها در چسب رخ می دهد. پخت چسب های آکریلیکی در دمای اتاق و با سرعت مطلوب انجام می شود و برای اتصال فلزات، کامپوزیت ها، پلاستیک ها و … مناسب هستند. منحصر به فرد بودن آن ها برگرفته از پخت سریع آن ها در دمای اتاق است. مقاومت خوب کششی، برشی، مقاومت در برابر ضربه و مقاومت شیمیایی مطلوب از دیگر ویژگی این چسب های ترموست است. در چسب های آکریلیک فرآیند پخت به روش پلیمریزاسیون رادیکال های آزاد (Free radical polymerization) انجام می شود. در حالی که مکانیسم پخت در چسب های پلی اورتان و اپوکسی، پلیمریزاسیون تراکمی (Condensation Polymerization) است.
بیشتر بدانید : آشنایی با چسب های بر پایه حلال
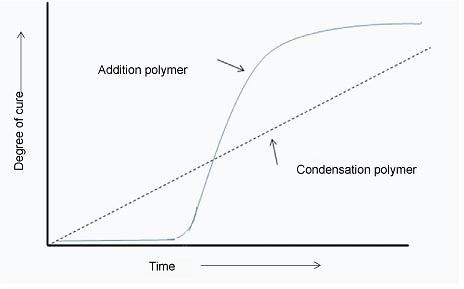
تفاوت میان این دو مکانیسم در نمودار روبرو قابل مشاهده هستند :
پخت چسب های اپوکسی و پلی اورتان در دمای اتاق چند روز یا هفته به طول می انجامد این در حالی است که آکریلیک های ترموست در عرض چند ساعت به پخت ۱۰۰% می رسند. مدت زمان قابلیت مصرف پس از اختلاط دو جز یا Pot life در چسب های آکریلیک، نسبت به اپوکسی و پلی اورتان بیشتر بوده و ویسکوزیته به تدریج افزایش می یابد. این افزایش تدریجی ویسکوزیته منجر می شود تا آکریلیک به درز ها و شکاف ها و هرگونه حفره و زبری در مقیاس میکرو نفوذ کند. کند بودن پلیمریزاسیون در ابتدای کار و در مراحل اولیه، امکان جابه جایی بسترها و قرار دادن آن ها در موقعیت مورد نظر را برای ما فراهم می سازد.
طریقه ی استفاده از این چسب ها می تواند مشابه با روش به کارگیری چسب های ساختاری و یا کاملا متفاوت از آن ها باشد. در روش اول، دو جز سیستم می توانند با دست و یا با استفاده از دستگاه پیش از استفاده مخلوط شوند. در روش دوم یکی از اجزا بر روی یک بستر و جز دیگر بر روی بستر دوم اعمال می شود. پلیمریزاسیون با اتصال دو بستر به یکدیگر و تماس دو جز آغاز می شود. در روش سوم که به ندرت به کارگرفته می شود، اجزای پایه ی (پلیمر پایه که متشکل از مونومر ها و سخت کننده است) بر روی یک بستر و یک محلول پرایمر فعال کننده واکنش بر روی بستر دیگر اعمال می گردد. حلال موجود در پرایمر تبخیر شده و ترکیب فعال کننده وابسته به ماهیت شیمیایی خود در حالت مایع یا جامد بر روی بستر باقی می ماند.
مقاومت کششی بالا و انعطاف پذیری بیشتر نسبت به چسب های اپوکسی، و استحکام پیوندی خوب به بسترهای پلیمری از ویژگی های منحصر به فرد این چسب ها هستند.
بیشتر فلزات به دلیل تاثیری مشابه با یک کاتالیزور بر روی مکانیسم پخت رادیکال های آزاد، موجب تسریع پخت چسب های آکریلیک حرارتی می شوند. آکریلیک های حرارتی در برابر آلودگی سطوح نیز مقاوم هستند و نیازی به آماده سازی بسترها نیست. اتصال بسترهای فولادی آغشته به روغن به راحتی به وسیله ی این چسب ها امکان پذیر است. تصور بر این است که روغن در داخل پلیمر توزیع شده و به عنوان یک روان کننده یا نرم کننده عمل می کند. این یک مزیت بزرگ در اتصال سطوح بزرگ فولادی در صنعت است. چرا که سطوح یزرگ فولادی به منظور جلوگیری از خوردگی عموما آغشته به روغن هستند.
حداکثر دمای عملیاتی در استفاده از آکریلیک های حرارتی، در صورت کوتاه بودن بازه ی زمانی C ˚ ۱۲۰ و در صورت پیوسته بودن حرارت C ˚ ۱۰۴ است. ترکیب این چسب با رزین اپوکسی می تواند منجر به افزایش دمای عملیاتی تا C ˚ ۱۷۵ شود. در دماهای پایین نیز تا دمای C ˚ ۴۰- عملکرد خوبی دارند.
از جمله حلال های رایج در تولید این چسب ها اتانول(ethanol)، استون(acetone)، اتیل استات، متیل استات، بوتیل استات(butyl acetate)، تولوئن(toluene)، زایلن(xylene) و اتیل لاکتات(ethyl lactate) هستند. استفاده از حلال های با فراریت بالا مانند استون موجب نفوذ کمتر رزین در مواد شده و استفاده از حلال هایی با فراریت کمتر مانند تولوئن درجه نفوذ رزین را افزایش می دهد.
کاربرد :
- صنعت حمل و نقل (کامیون، اتومبیل، اتوبوس و صنایع دریایی …)
- تولید تجهیزات ورزشی مانند چوب های گلف
- تولید تابلوهای تبلیغاتی
- اتصال و آب بندی پنجره ها
- تولید صفحات نمایشگر تلویزیون (LCD)
- تیغه ی توربین های بادی
- اتصال قطعاتی مانند روتور، شفت و آهنربا در فرآیند تولید موتورهای الکتریکی
- در سیم پیچی ترانسفورماتورهای فریت(Ferrite )
- اتصال بسترهای پلاستیکی ضعیف از جمله بسترهای پلی پروپیلن، پلی اتیلن و پلی الفین های ترموپلاستیک که دیگر چسب ها قادر به اتصال آن ها نیستند.
- اتصال صفحات نازکی از فلزات مانند آلومینیوم و فولاد، و پلاستیک های مهندسی(Engineering plastic)
- چسباندن آهنربا در وسایلی مانند اسپیکرها
- اتصال پلاستیک هایی مانند ABS، آکریلیک، پلی کربنات، PVC، نایلون، رزین فنولی، اپوکسی و ملامین
اتصال آکریلیک پلی متیل متاکریلات به وسیله ی چسب آکریلیک سیانوآکریلات
Ferrite : فِرّیتها، مواد سرامیکی هستند که از ترکیب اکسید آهن و فلزهای دو ظرفیتی مانند باریم، استرانسیم، سرب، نیکل، کبالت و … ساخته میشوند. فریتها جزء مواد فِرّیمغناطیسی هستند. آنها سخت و شکنندهاند و رنگشان خاکستری یا سیاه است.
تاریخچه :
در سال ۱۹۰۱ در توبینگن(Tuebingen) آلمان، یک کاندید دکتری به نام Otto Rohm پایان نامه ای در رابطه با توصیف محصولات حاصل از میعان سدیم آلکوکسید(sodium alkyoxides) با متیل و اتیل آکریلات منتشر کرد. او در این مقاله درباره ی ماهیت شیمیایی مواد پلیمری که هم زمان در این واکنش تشکیل شده اند نیز مطالبی را عنوان کرده است. دکتر روم با این کار توانست تحول بزرگی در صنعت شیمیایی ایجاد کند. نتیجه ی این تحول دستیابی به چسب ها، پلاستیک ها، پوشش دهنده ها، رزین ها و … در طول نیم قرن بود. در طول این نیم قرن فرآیندهایی برای تولید مونومرهای آکریلات و انواع مواد پلیمری که از آن مونومرها به دست می آیند، ابداع شدند. این چسب ها از دهه ی ۱۹۶۰ به صورت تجاری وارد بازار شده اند.
مزایا و معایب :
معایب :
- بوی نامطبوع مونومر
- قابل اشتعال بودن
- در برخی از پلاستیک های خاص می تواند موجب ترک خوردگی تنشی شود.
- مقاومت محدود در برابر حلال های قطبی مانند استون، محلول های اسیدی و یا باز قوی
- در استفاده برای بسترهای از جنس روی ممکن است به پرایمر نیاز داشته باشیم.
مزایا :
- پخت سریع و قابل کنترل در محیط و دمای اتاق
- عدم نیاز به آماده سازی سطح
- قابلیت اتصال به سطوح مختلف مانند کامپوزیت، پلاستیک، فلز و …
- مقاومت زیاد در برابر فرسودگی
- مقاومت عالی در برابر ضربه
- دوام طولانی مدت
- خاصیت کشسانی بالا
- مقاوم بودن نسبت به آلودگی سطحی
- جامد بودن
- ضد خوردگی بودن
- قابلیت کاربرد و استفاده به روش های مختلف
- لازم نبودن نسبت های اختلاط دقیق
- قابلیت پرکردن تمام شکاف های کوچک و بزرگ
- مقاومت خوب در برابر رطوبت و فضای باز
- استحکام پیوندی مناسب در اتصال به بسترهای مختلف
- اتصال خوب به بسترهای فلزی مانند فولاد، آلومینیوم و مس
اجزای سازنده :
مهم ترین اجزای سازنده چسب های آکریلیک، مونومرها، کاتالیزور و سخت کننده ها هستند. ترکیبات یک چسب ساختاری در جدول زیر نشان داده شده است :
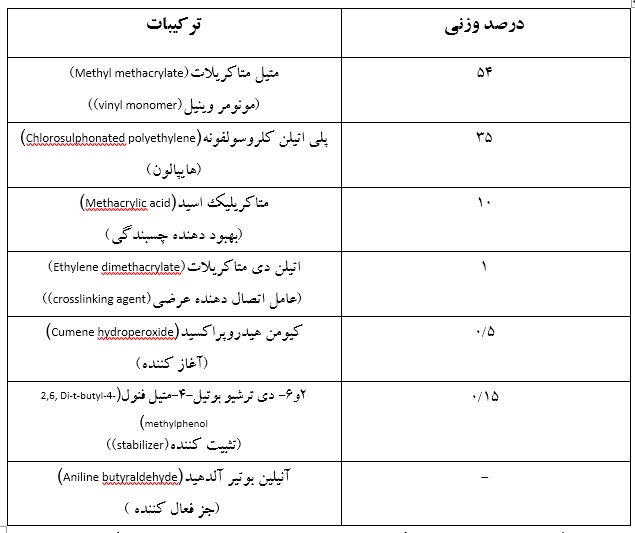
به طور کلی چسب به عنوان یک سیستم دو جزئی در نظر گرفته می شود. جز اول که به عنوان جز پایه در نظر گرفته می شود شامل مونومرها و آغاز کننده ها و مولفه دوم که به عنوان جز فعال کننده در نظر گرفته می شود شامل ترکیبات پخت شونده (curative) است. طیف گسترده ای از مونومرهای قابل پلیمریزاسیون مانند متیل متاکریلات(methylmethacrylate)، اتیل متاکریلات(ethyl methacrylate) ،دواتیل هگزیل متاکریلات(۲-Ethylhexyl methacrylate)، سیکلو هگزیل متاکریلات(cyclohexyl methacrylate) و اتیل آکریلات(ethyl acrylate) در چسب های آکریلیک حرارتی استفاده می شوند. در این بین متیل متاکریلات مقرون به صرفه ترین مونومر است. هرچه زنجیره ی مونومرها طولانی تر باشد، انعطاف پذیری و مقاومت افزایش می یابد. افزودن مونومرهای اسیدی به دیگر مونومرها مانند متاکریلیک اسید(methacrylic acid) می تواند موجب افزایش سرعت پخت، افزایش استحکام پیوند ها و مقاومت در برابر دما می شود. برای کاهش بوی چسب بهتر است از مونومر های با فعالیت کمتر[(Lower volatility monomers)استفاده شود. آن ها پلیمرهای گران قیمت تری هستند که عملکرد ضعبف تری در پخت، اتصال به پلاستیک ها و مقاومت نسبت به دما دارند. راه کار دوم برای کاهش بو، استفاده از واکس های پارافینی است.
در انتخاب کاتالیزور معمولا از پراکسیدهای آلی(organic peroxides)، هیدرو پراکسیدهای آلی(organic hydroperoxides)، پراسترها (peresters)، پر اسیدها(peracids) یا ترکیبات آزو (azo compounds) استفاده می شود. سایر ترکیبات در جدول زیر نشان داده شده است :

از کاتالیست های رایج بنزیل پراکسید(benzyl peroxide) به عنوان یک جز آغازکننده یا اکسید کننده و یک ترتیاری آمین (tertiary amine) (عموما دی متیل آنیلین(N,N-dimethylaniline)) به عنوان یک عامل پخت یا یک کاهنده هستند. دی اتیل آنیلین (Diethyl aniline) و دی متیل پارا تولودین(N,N-dimethyl-p-toludiene) از جمله فعال کننده ها هستند. نوع و غلظت فعال کننده بر سرعت پخت، گرمای آزاد شده و ثبات فرمولاسیون تاثیر می گذارد. منبعی از رادیکال های آزاد مانند بنزیل پراکسید (benzyl peroxide) در مراحل بعد در فرآیند مخلوط شدن اضافه می شوند. عموما از یک ماده ی حامل مایع غیر فعال مانند دی گلیسیدیل اتر بیسفنول آ (DGEBA) (Bisphenol A diglycidyl ether)یا یک روان کننده ی آلی(organic plasticizer) به منظور حفظ ثبات ترکیب استفاده می شود.
در برخی از موارد رادیکال های آزاد آغاز کننده یک جز اصلی از اجزای پایه ی چسب هستند در حالی که عامل پخت به صورت جداگانه یا به صورت محلول در یک حلال فرار بر روی بستر اعمال می شوند. به طور مثال در ترکیب بنزوئیل پراکسید و ترتیاری آمین(tertiary amine)، آمین جزئی از چسب بوده و بنزوئیل پراکسید بلافاصله قبل از استفاده با چسب ترکیب می شود. به طور کلی مونومرهای آکریلیک ذاتا ناپایدار هستند و از رادیکال های آزاد تثبیت کننده برای نگهداری و تثبیت آن ها استفاده می شود. غلظت آن ها به تنهایی برای نگهداری و ذخیره سازی چسب های ترموست به ویژه فرمولاسیون هایی که در آن از کاتالیست پراکسید استفاده می شود، کافی نیست. بنابراین نیاز است که از تثبیت کننده های رادیکال آزاد(free radical stabilizers) مانند هیدروکینون(hydroquinone)، متیل هیدروکینون((methyl hydroquinone (MHQ)، ۲و۶- دی ترشیو بوتیل-۴- متیل فنول (BHT(2,6-Di-tert-butyl-4-methylphenol) و پارا بنزوکینون(p-benzoquinone) استفاده شود. در این بین BHT بدون تحت تاثیر قرار دادن سرعت پخت، ماندگاری را افزایش می دهد. از آنجایی که تثبیت کننده ها در فاز جامد قرار دارند، بهتر است در ابتدای فرآیند اختلاط به منظور حل شدن کامل در مخلوط، افزوده شوند.
برای سرعت بخشیدن به نرخ فرآیند پخت در دمای اتاق، از شتاب دهنده هایی بر پایه ی نمک های آلی فلزات واسطه(transition metals) مانند مس یا نفتنات کبالت(cobalt naphthenate)، اکتوات ها(octoates)، استیل استانوآت(acetylacetaonates) و هگزوآت های(hexoates) فلزات واسطه استفاده می کنند که می توانند به ماده پخت افزوده شوند. مشابه با فعال کننده ها(activators) بازده استفاده از این کاتالیزورها بر روی سرعت پخت، گرمای آزاد شده(exotherm) حاصل از آزمایش و پایداری چسب تاثیر می گذارد.
سخت کننده های(toughners)متنوعی در چسب های آکریلیک حرارتی استفاده می شوند. انتخاب سخت کننده عموما با در نظر گرفتن دمای انتقال شیشه ای و انحلال پذیری آن در مونومر انجام می شود. معمولا در ابتدای کار سخت کننده در مونومر حل می شود. برخی از این سخت کننده ها شامل پلی اتیلن کلروسولفون دار شده(Chlorosulfonated polyethylene)، پرکننده های هسته- پوسته(Core shell fillers)، نئوپرین یا پلی کلروپرن(Polychloroprene)، پلی بوتادین(Polybutadiene)، کوپلیمرهای پلی بوتادین/آکریلونیتریل(Polybutadiene / acrylonitrile copolymers)، الاستومرهای اورتان(Urethane elastomers)، الاستومرهای آکریلیک(Acrylic elastomers)، ترکیب پلی بوتادین/ایزوسیانات(Polybutadiene / isocyanate adduct)، وینیل های مختوم به بوتادین/آکریلونیتریل(Vinyl-terminated butadiene / acrylonitrile) و متاکریلات های پلی اورتان(Polyurethane methacrylates) هستند. در این بین پلی اتیلن کلروسولفوناته رایج تر است. مونومرهای وینیل با این پلی اتیلن ها برخورد کرده و یک پیوند شیمیایی مابین ماتریس شکننده و فاز الاستومری برقرار می شود. این پیوند شیمیایی سختی و دوام را در آکریلیک های تولید شده افزایش می دهد. پلیمرهای آکریلیک به طور گسترده برای ساخت چسب های حساس به فشار (PSAs) (pressure-sensitive adhesives)با مزایای منحصر به فرد ذاتی نسبت به دیگر چسب های بر پایه پلیمر استفاده می شوند.
تولید :
چسب های آکریلیک طی فرآیند پلیمریزاسیون رادیکال های آزاد مونومرهای آکریلیک تولید می شوند. مراحل این واکنش زنجیره ای شامل مرحله ی آغازین، انتشار و پایانی یا خاتمه است. آغاز کننده ها ترکیبات ناپایداری هستند که در دمای بالا تجزیه شده و رادیکال های آزاد (مولکول هایی با الکترون جفت نشد) تشکیل می دهند. رایج ترین مونومرهای آکریلیک استفاده شده در این فرآیند شامل آکریلیک اسید(Acrylic acid)، متیل آکریلات(Methyl acrylate)، اتیل آکریلات(Ethyl acrylate)، دو اتیل هگزیل آکریلات(- ۲‐Ethylhexyl acrylate)، متیل متاکریلات(Methyl methacrylate)، متاکریلیک اسید (MAA)(methacrylic acid)، نرمال بوتیل متاکریلات(n-BMA)(N-butyl-methacrylate)، ایزوبوتیل متاکریلات(iso-butyl methacrylate)، سیکلوهگزیل متاکریلات(CHMA)، ۲- (cyclohexyl methacrylate)هیدروکسی اتیل متاکریلات(۲-hydroxyethyl methacrylate) 2- اتیل هگزیل متاکریلات و آکریلونیتریل(Acrylonitrile)رایج ترین رادیکال های آزاد آغازین شامل ۲و’۲-آزوبیس ایزو بوتیرونیتریل (AIBN)(2,2’‐Azobisisobutyronitrile (AIBN))، ترت- بوتیل پراکسید(tert‐Butyl peroxide)، کیومیل پراکسید(Cumyl peroxide)، بنزوئیل پروکساید(Benzoyl peroxide)، ترت – بوتیل هیدروپراکساید( tert‐Butyl hydroperoxide) و ترت- بوتیل پربنزوئات(tert‐Butyl perbenzoate) هستند. ترکیب مونومر متیل متاکریلات با دیگر مونومرها موجب دستیابی به خواص مکانیکی و ترموفیزیکی بهینه می شود. به طور کلی بوی کمتر متاکریلات ها موجب شده تا نسبت به آکریلات ها ترجیح داده شوند.
گروهی دیگر از چسب های آکریلیک ترموست، که با نام چسب های آکریلیک فعال( reactive acrylics) یا چسب های متاکریلیک(Methacrylic adhesives) شناخته می شوند از مونومرهایی مشابه با چسب های بی هوازی تشکیل می شوند. فرمولاسیون دقیق آن ها موجب شده تا در فضای باز نیز فرآیند پخت انجام شود. در این چسب ها معمولا از سخت کننده های لاستیکی، مشابه آنچه در چسب های اپوکسی استفاده می شود، برای بهبود مقاومت و انعطاف پذیری چسب های شکننده ی بر پایه ی متاکریلات استفاده می شود. منومرهای متاکریلات معمولا با آغازکننده(initiator) های پر اکسید(peroxide) یا هیدروپراکسید(hydroperoxide) پخته می شوند. فرآیند پخت در این سیستم ها به آرامی صورت گرفته و نیاز است که از یک آمین نوع سوم برای افزایش سرعت پخت استفاده شود. فرآیند پخت می تواند بسته به نوع رزین آکریلیک استفاده شده، غلظت پراکسید و شتاب دهنده در عرض چند دقیقه یا چند ساعت در دمای اتاق اتفاق می افتد.
در تولید چسب های آکریلیک حساس به فشار برای حل کردن مونومرهایی مانند ۲- اتیل هگزیل آکریلات، متیل متاکریلات و آکریلیک اسید از حلال های آلی مانند اتیل استات(ethyl acetate)، تولوئن(toluene)، ایزوپروپیل الکل(isopropyl alcohol)، هپتان(heptane) و متیل اتیل کتون (MEK) (Methyl Ethyl Ketone)استفاده می کنند. در میان این حلال های آلی اتیل استات، از رایج ترین آن ها است. این کوپلیمرهای آکریلیک جامد درون همزن با حلال اتیل استات مخلوط شده و رقیق می شوند. از این چسب های حساس به فشار عمدتا در تولید صفحات محافظ بر روی نمایشگرهایLCD (liquid crystalline displays)استفاده می شود.